Unlocking Precision with a Lathe Machine Parts Factory
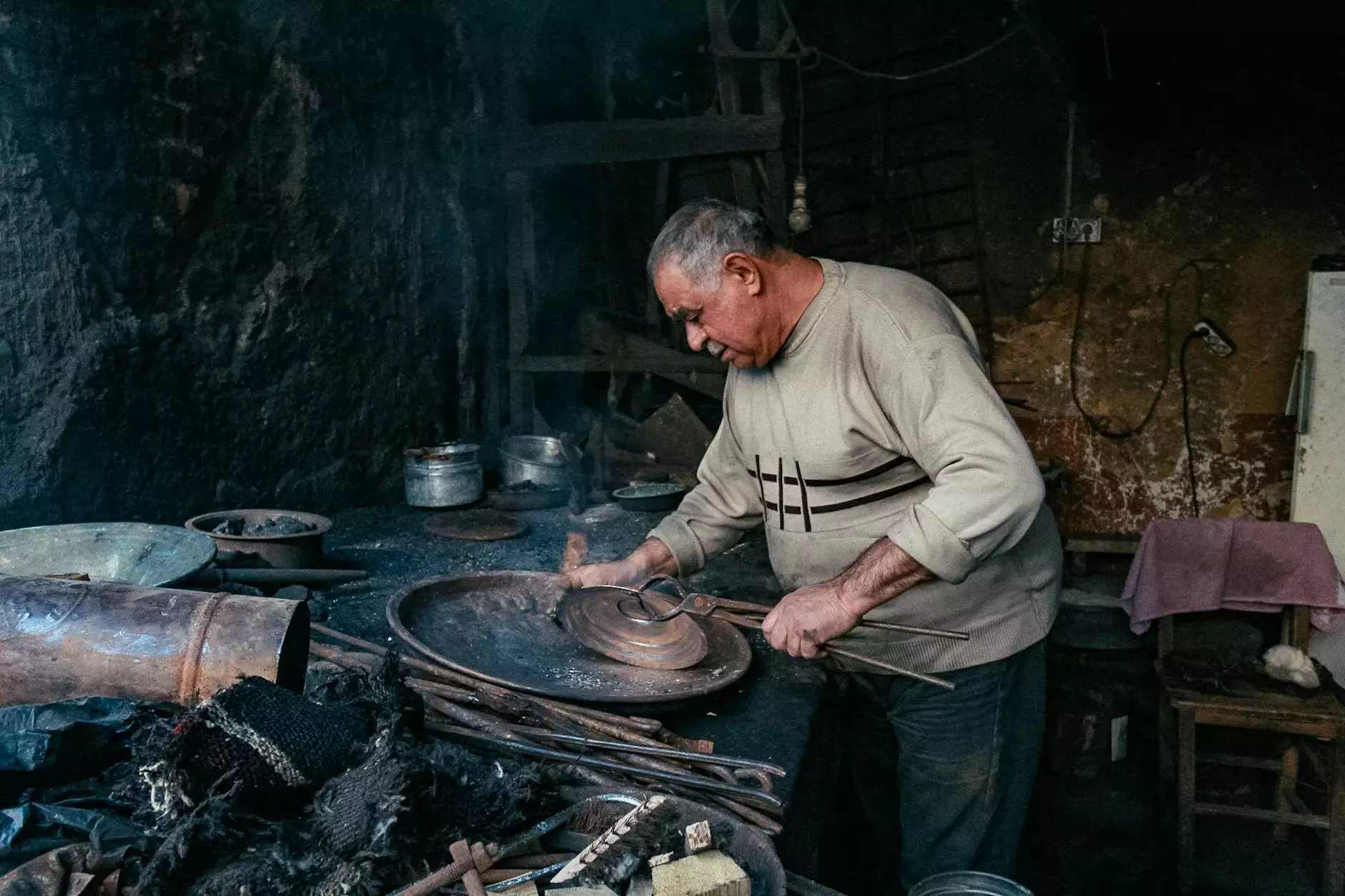
In today’s fast-paced industrial landscape, the demand for precise and reliably manufactured parts is more critical than ever. At the heart of this manufacturing revolution lies the lathe machine parts factory, an essential player in the metal fabrication industry. This article delves into the integral role that these factories play, the processes involved, and how businesses can leverage their capabilities for growth and innovation.
The Significance of Lathe Machines in Manufacturing
Lathe machines are one of the oldest and most versatile tools in manufacturing. They allow for the precise machining of various materials, including metals, plastics, and composites. By rotating a workpiece against cutting tools, lathe machines can create intricate shapes with high levels of accuracy. This functionality makes lathe machine parts crucial for several applications.
Core Applications of Lathe Machines
- Automotive Industry: Manufacturing components like shafts, spindles, and crankshafts.
- Aerospace Sector: Producing high-precision parts that meet stringent regulations and quality standards.
- Medical Devices: Crafting precise instruments and surgical fixtures that require a high degree of accuracy.
- Consumer Goods: Manufacturing decorative items and functional components for various products.
How a Lathe Machine Parts Factory Operates
A lathe machine parts factory typically involves a series of well-coordinated processes that ensure quality and precision in every component produced. Here is a closer look at how these factories operate:
1. Design and Engineering
The journey of part manufacturing starts with effective design and engineering. Skilled engineers utilize advanced CAD (Computer-Aided Design) software to create detailed 3D models that ensure the parts meet the required specifications. This step is crucial as it lays the foundation for the precision and functionality of the end product.
2. Material Selection
Choosing the right material is vital for the performance of the manufactured parts. Common materials used in lathe machining include:• Steel• Aluminum• Brass• Plastic
The selection process takes into account factors such as strength, weight, and corrosion resistance to ensure the part meets its intended use.
3. Machining Process
Once the designs are finalized, the lathe machining process begins. The selected material is mounted on the lathe, and various cutting tools are used to shape the material into the desired form. This may involve:
- Turning: Removing material from the outside diameter to create cylindrical parts.
- Facing: Cutting the ends of the workpiece to create flat surfaces.
- Drilling: Creating holes in the material for assembly or weight reduction.
- Tapering: Shaping the workpiece to create a conical form.
4. Quality Control
Quality control is an integral aspect of the manufacturing process. After machining, parts are subjected to rigorous testing procedures to ensure they adhere to exact specifications. This may include:
- Dimensional Inspection: Checking dimensions with precision instruments.
- Surface Finish Testing: Ensuring the surface quality is as required.
- Functional Testing: Assessing the part's performance in its intended application.
Benefits of Partnering with a Lathe Machine Parts Factory
Businesses that partner with a lathe machine parts factory can reap numerous benefits. Let’s explore some of the key advantages:
1. Cost Efficiency
Outsourcing part production to a specialized factory can significantly reduce operational costs. Factories that focus on lathe manufacturing benefit from economies of scale, optimizing production processes and minimizing waste.
2. Enhanced Quality
By leveraging the expertise and advanced technologies of a lathe parts factory, businesses can achieve a higher level of quality in their products. This not only improves customer satisfaction but also bolsters brand reputation.
3. Access to Expertise
Manufacturers gain access to skilled professionals with vast experience in machining and design. This expertise can facilitate quicker problem solving and innovation in product development.
4. Scalability
Partnering with a lathe machine parts factory offers scalability options. As a business grows, the factory can adapt to increased production demands without the need for substantial investments in machinery or workforce.
Conclusion
In conclusion, lathe machine parts factories are essential components of the modern manufacturing ecosystem. They provide a crucial service that supports various industries by delivering high-quality, precision-engineered parts. By understanding the operations and benefits of these factories, businesses can make informed decisions about their manufacturing processes and forge fruitful partnerships that drive success.
As a leading metal fabricator, Deep Mould (available at deepmould.net) specializes in offering top-tier lathe machine parts, ensuring that our clients receive the quality and precision they require. Investing in a lathe machine parts factory partnership means investing in the future of your business.
Get Started with Lathe Machine Parts Today!
For businesses looking to enhance their manufacturing process, connecting with a reputable lathe machine parts factory is essential. Contact Deep Mould today to learn how our services can meet your specific needs and help you achieve excellence in your operations!