Understanding Injection Moulding Tooling for Metal Fabricators
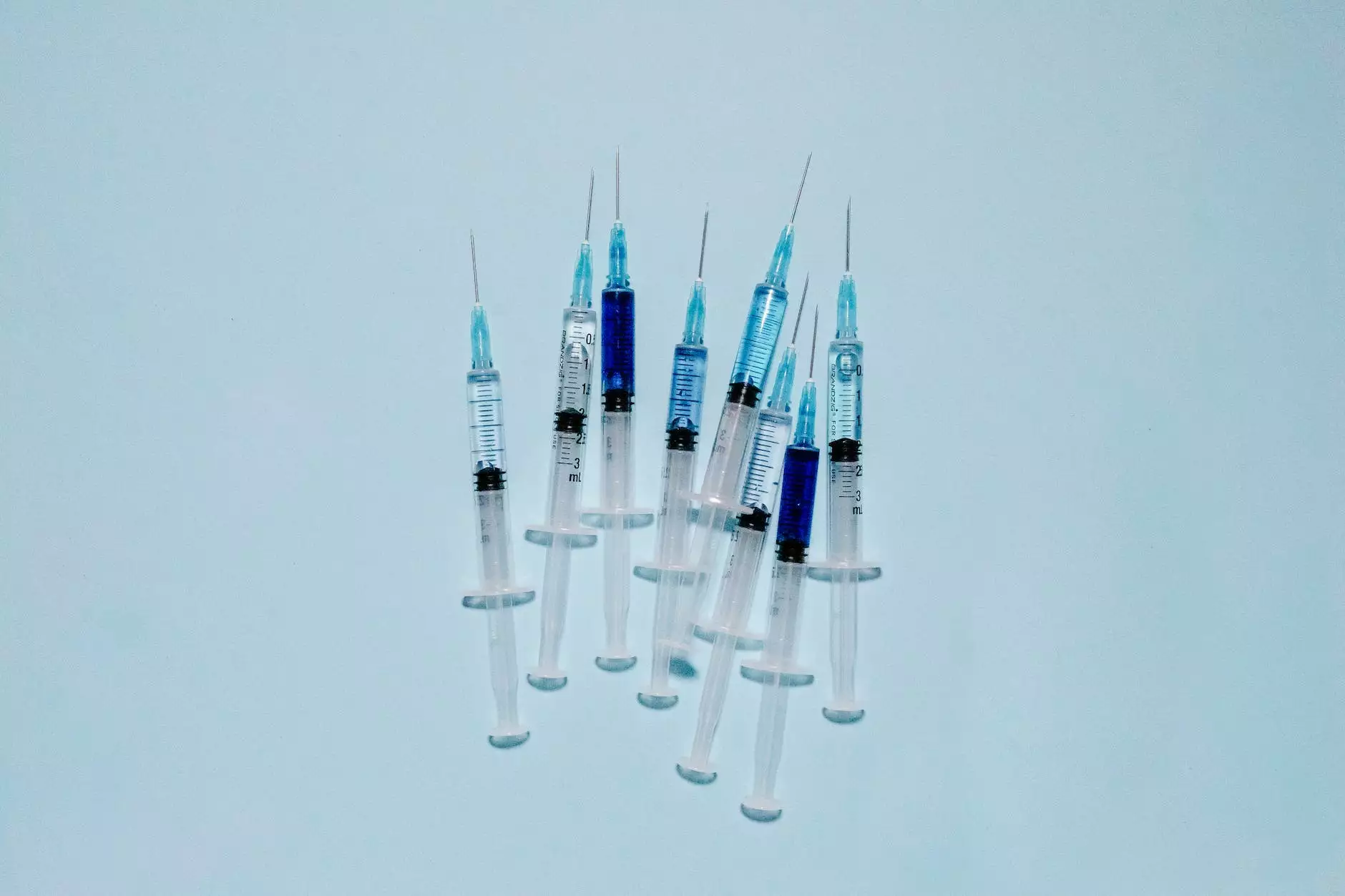
Injection moulding tooling is a critical component in the manufacturing landscape, particularly in the realm of metal fabrication. In this comprehensive guide, we will delve into the intricate details surrounding injection moulding, its processes, and the vital role it plays in producing high-quality metal products. This article aims to equip business owners and manufacturers, like those at deepmould.net, with the knowledge needed to excel in this area.
What is Injection Moulding Tooling?
At its core, injection moulding tooling refers to the set of tools used to create moulds for the manufacturing process of various items, predominantly plastic and metals. This process involves injecting molten material into a mould cavity, where it cools and solidifies into the final product. The tooling aspect is crucial, as the quality and design of the mould directly affect the end product's features and performance.
The Importance of Quality Tooling
In the competitive world of metal fabrication, producing reliable and high-quality products is non-negotiable. Quality tooling in injection moulding ensures:
- Precision: High-quality moulds lead to exact specifications, enabling the production of intricate designs.
- Durability: Well-made tools stand up to the rigors of the injection process, reducing wear and tear.
- Cost-Effectiveness: Investing in superior tooling can minimize production errors and material wastage, ultimately reducing costs.
- Speed: Efficient tooling can increase production speed, allowing businesses to meet demand without sacrificing quality.
Types of Injection Moulding Tooling
The realm of injection moulding tooling is diverse, encompassing various types of moulds tailored to specific applications:
1. Single Cavity Mould
This type of mould produces one part per cycle and is often used for low-volume products. Single cavity moulds are cost-effective and simple to design.
2. Multi-Cavity Mould
In contrast, multi-cavity moulds can produce multiple parts in a single cycle, enhancing efficiency and driving down costs for high-volume production. This type is ideal for items that require uniformity across batches.
3. Family Mould
Family moulds are designed to produce different parts simultaneously. This strategy is beneficial for companies seeking to optimize production lines for varying products.
4. Hot Runner Mould
Hot runner moulds maintain the molten state of the plastic before it enters the cavity, reducing waste and enhancing productivity.
5. Cold Runner Mould
Cold runner moulds, on the other hand, are simple but can result in higher material waste. A good understanding of these types helps businesses choose the right tooling for their specific needs.
Factors Influencing Injection Moulding Tool Design
Designing injection moulding tools involves several critical considerations. Each factor is unique and influences the overall efficiency and effectiveness of the production process:
- Material Selection: The types of materials used (metals, plastics, etc.) directly affect the design and functionality of the mould.
- Mould Configuration: The intricacies of the design, such as wall thickness or the presence of undercuts, determine the complexity of the tooling process.
- Cooling System Design: Effective cooling is essential for reducing cycle times and ensuring the quality of the final product.
- Finish Requirement: The desired finish of the product will dictate the surface treatment and texturing of the mould.
- Production Volume: Higher volumes may require more durable, complex tooling, while lower volumes might prioritize cost-efficiency.
Benefits of Injection Moulding Tooling in Metal Fabrication
The benefits of integrating quality injection moulding tooling in metal fabrication are substantial:
- Enhanced Production Capability: With the right tooling, manufacturers can produce high volumes efficiently.
- Improved Quality Control: Moulds that are well-designed foster consistent production standards, reducing defects.
- Greater Design Flexibility: Advanced tooling allows engineers to execute complex designs and innovations, keeping businesses competitive.
- Shorter Time to Market: Efficient moulding processes enable quicker turnaround times from concept to final product.
Choosing the Right Injection Moulding Tool Provider
When selecting a provider for your injection moulding tooling, consider the following factors:
- Experience and Expertise: Look for a company with a strong background in the industry and a proven track record.
- Technological Investment: A provider that invests in state-of-the-art technology can offer superior tooling solutions.
- Customer Support: Quality customer service is vital to address any issues or concerns arising during production.
- Portfolio Review: An evaluation of past projects can provide insight into the provider's capabilities and reliability.
The Future of Injection Moulding Tooling
The future of injection moulding tooling is bright, influenced largely by technological advancements and evolving market needs. Here are some trends to watch:
- Automation and AI: Integrating AI solutions into the tooling process can optimize production flows and reduce overall costs.
- Sustainability Practices: As environmental consciousness grows, expect an increase in sustainable materials and methods in tooling.
- 3D Printing Technology: The rise of 3D printing technologies is reshaping mould design, offering customization and rapid prototyping opportunities.
- Smart Manufacturing: The digitalization of manufacturing processes will enhance tracking and quality control of injection moulding tooling.
Conclusion
The realm of injection moulding tooling is expansive and intricately linked to the success of metal fabricators. By understanding the various elements at play, businesses can make informed decisions that enhance production efficiency, quality, and innovation. At deepmould.net, we are committed to providing high-quality tooling solutions that meet the evolving demands of the industry. Through well-designed tooling, metal fabricators can tap into improved capabilities, ensuring they remain competitive and capable of meeting their customers' needs. As the industry evolves, staying ahead of technology trends will keep businesses prepared for future challenges and opportunities.